There are numerous learnings that occur with years of experience and abundant project involvements. Last month, the lessons of effective communications and product definition were discussed. This month, the learnings from project planning and project execution are the focal points.
Planning
Only slightly behind communication in the importance spectrum is planning. However, planning is the phase of the project that most people want to avoid or skip because it takes time and many outsiders don’t see action or visible progress. Just remember, “Failing to plan is planning to fail”. Hope is NOT a plan!
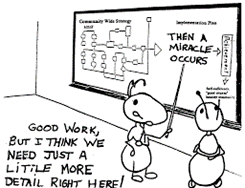
A general building contractor would not begin building a house without a blueprint and other site preparation activities; similarly, new product development requires vetted product requirements and a detailed development plan so that progress can be tracked and problems avoided.
Take time at the beginning of a project to orient the team to the objectives of the client or sponsor. With this background knowledge, the team is also able to define the right balance of time, cost, and features. Likewise establishing team member roles and responsibilities at the onset helps everyone know what is expected and by whom. Once the team knows the project objectives and the position they play to fulfill those objectives, they can contribute quickly and confidently. The team can make or break the project outcome; therefore, having a cohesive team heightens the chances that misunderstandings will be avoided and challenges will be addressed in a timely manner.
Furthermore, make sure that the team has a holistic overview of the client’s project completion objectives. This “definition of done” may include understanding the documentation needed to meet the organizational requirements, understanding the industry standards that must be met, or understanding the manufacturing needs to build the device being designed.
Begin With the End
I’ve found that one of the most effective planning approaches is to begin with the end in mind. This technique helps the team focus on the project objective and allows the team to decompose the key aspects of the project. It also can be a tool to “park” (set aside) distracting tasks that may cloud the team’s ability to focus on the critical work tasks.
During the planning phase, be cautious of locking in “the solution” too early. Consider various options and perform some rudimentary research for alternative solutions. By comparing and contrasting concepts (see Pugh’s concept selection method) the team may be able to derive a hybrid concept that will utilize the strengths of two or more base concepts.
The person closest to the work should provide the cost and time estimates but, as stated by one of my colleagues, estimates are wrong by definition. Therefore, take into consideration the experience that the person providing the estimates has with estimating. Some people are overly optimistic, others pad their estimates so they have plenty of headroom. Consequently, if possible, it’s recommended that multiple estimation methods be utilized when creating development costs and timelines. Estimation methods may include top-down planning, bottom-up planning, analogous, parametric, or three-point estimation.
Expect the Unexpected
Another critical facet during project planning is to define contingencies since new product developments rarely go 100% according to plan. All product developments have some areas of risks as well as details that can’t be known until the development reaches further levels of maturity. Therefore, review those areas of development that have never been done before, either by the industry at large or by the development team, and plan for alternative methods to accomplish the work objectives in the event the primary path becomes blocked. In addition, expect the unexpected when accounting for risks and contingencies. In other words, perform “what if” scenarios to uncover potential risks.
One way to manage risks is to break large efforts into several smaller efforts. This allows for more focused planning of each of the smaller efforts and allows problems to be discovered sooner rather than later. This concept is the premise behind many of the agile methodologies being currently adopted by many organizations. The technique can be very effective when beginning a project with a new supplier because it allows the contract letting organization limit their exposure while building a rapport between the two businesses. Another means to minimize risk is to reuse previous known design components whenever possible. This practice eliminates the unknown risks and reduces the time needed to bring functionality to a device.
Leading Edge Technology
Be cautious when incorporating new technology and/or standards into a device. It’s OK to use “leading edge” technologies, but not “bleeding edge” technologies that can make a schedule very unpredictable. If it’s decided to use technologies or standards that are first in the industry, allow for contingency time and funding – you’ll need it! I recall a project where it was decided that the newly coined Bluetooth Low Energy (BLE) technology HAD to be Continua compliant (a new communication standard used in the medical community). The team had numerous obstacles to implement both of these requirements. Obtaining parts from suppliers was next to impossible and no pre-existing firmware stacks were available to accelerate the implementation. Coupled with this challenge was a newly evolving industry standard that had never been empirically verified. Therefore, when the team finally had a physical device to be certified to the standard, there were no test houses prepared to certify the device! In the end, these requirements cost the team weeks of development along with thousands of dollars before the product manager conceded to jettisoning the requirements.
Lastly, know when a project is not ready to begin development! Some project ideas/needs are at the invention or science-fair stage of the process and therefore discovery/research or proof-of-concept work is needed before applicable requirements can be defined for product development. If a product architecture cannot be confidently described indicating how the product functions/features will be delivered, then the project is not ready to advance into development.
Project Execution
Remember that planning is good but the plan is only worthwhile if it is followed. For the plan to be effective, someone must monitor the designated project performance metrics against the plan as the project progresses. Armed with this knowledge the team and the client will be aware of the next actions needed to achieve the project objectives.
It is indispensable to have a defined development process to help guide and navigate the development activities. However, I’ve discovered that there are some non-documented process tips that can improve the chances that the development will progress well. When developing a new product, develop the primary function of the product FIRST. If the device is measuring a medical assay, make sure the measurement system performs as expected before worrying about ancillary functions like communicating to external systems. However, if the device is a wireless communication mechanism, confirm that it reliably transmits and receives data before focusing on product functions that are not performed wirelessly.
Mock-Up Design Concepts
If possible, mock-up critical design concepts using rapid prototyping methods. Often a design can look great on a computer model but a physical model will reveal considerations that the computer model cannot. Finding these considerations at the beginning of the design process allows more options for changes and reduces the need for redesign efforts which can save significant time and cost. Creating rapid models can provide a wealth of knowledge.
Always, verify the work as early as possible. Although design verification is a key element in any development process, it’s best to perform verification tasks as soon as a design element is mature enough to test, even if it’s informally. Don’t wait until the whole design is complete to start testing. In so doing, opportunities are created to find non-desirable characteristics early such as the connectors between PCB 1 and PCB 2 are mirror-imaged due to a layout error and therefore don’t integrate properly. By the way, don’t forget to allocate materials in the planning process to account for these testing efforts.
Fix Any Issues Immediately
Inevitably, an issue will surface during development. When an issue surfaces, fix it now. Similar to the point made in the previous post about difficult conversation, issue resolution requires urgency or the problem may grow to a point where the entire project is derailed.
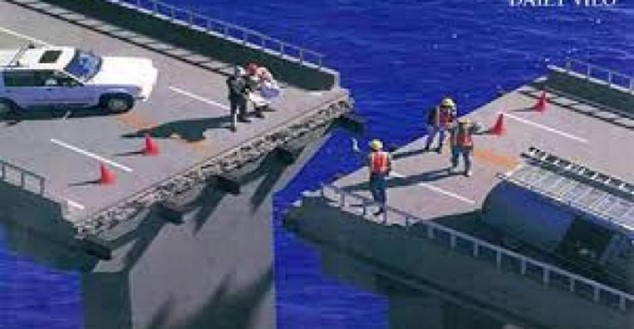
Don’t forget to involve manufacturing professionals during the design phase. A smooth transition between the design team and the manufacturing team occurs by interacting and collecting input from the manufacturing team early. Manufacturing engineers can guide and assist designers in finding ways to produce the device in the most economical way possible. They also understand assembly processes and factory capabilities in more depth than a design engineer. Therefore, collaborating with them while the design is in its infancy can lead to an easy design transfer exchange which will save time and costs initially and will continue to yield dividends due to lower manufacturing costs.
Manage Risks
Another process area that can go unattended but can make a significant difference in the project success involves managing risks. New product development is risky just because in most cases the team is creating something that doesn’t already exist therefore the team frequently doesn’t know what it doesn’t know. By capturing risks in a document along with mitigation strategies and consequence severity rankings, the team can periodically review the list of risks to minimize the potential of being sabotaged by the risk. Typically it takes some practice managing risks to know the sweet spot of what risks may be project impactors (or killers); however, the rewards for effectively managing risks can be significant.
Project execution is obviously where the “rubber meets the road”. Appropriate planning helps ensure good traction and creates a roadmap to follow to the destination. Periodically, the tires may slip or a detour will occur. It’s important to be prepared for these situations so that corrective actions can be taken without over-reacting. Along the journey, keep monitoring the dashboard so you know how much fuel is left and watch for warning lights to avoid ruining the engine.
What’s Next?
Next month’s article discusses the importance of team health and periodic reviews for successful outcomes. Company culture and technical depth have a significant impact on these factors so it’s important to consider them when selecting a design partner. As a testimonial to Indesign’s culture, the company has received the Best Places to Work in Indiana award for the last 11 consecutive years. In addition, Indesign clients benefit by being able to draw from the knowledge base and experience of over 50 seasoned engineers when conducting design reviews or finding solutions to technical obstacles. To learn more about us and our services, contact us at (317) 377-5450 today!